Focus Applied Technologies Dynamometer Testing at SEMA 2018
Once again, Focus Applied Technologies was at the Shell eco Marathon Asia this year with our Hypermileage Chassis Dynamometer testing both Urban Concept and Prototype cars. We ran the dyno for four days, with 44 total runs by various teams, some more than once and again have a perfect safety record. We were able to resolve over 80% of the problems, and happily there was much more tuning going on this year, and less fundamental problem solving compared to past years. We were even able to help out Shell and SwRI with some EMI (Electromagnetic Interference) and remote shut-down testing. A Pareto of the tests is shown below.
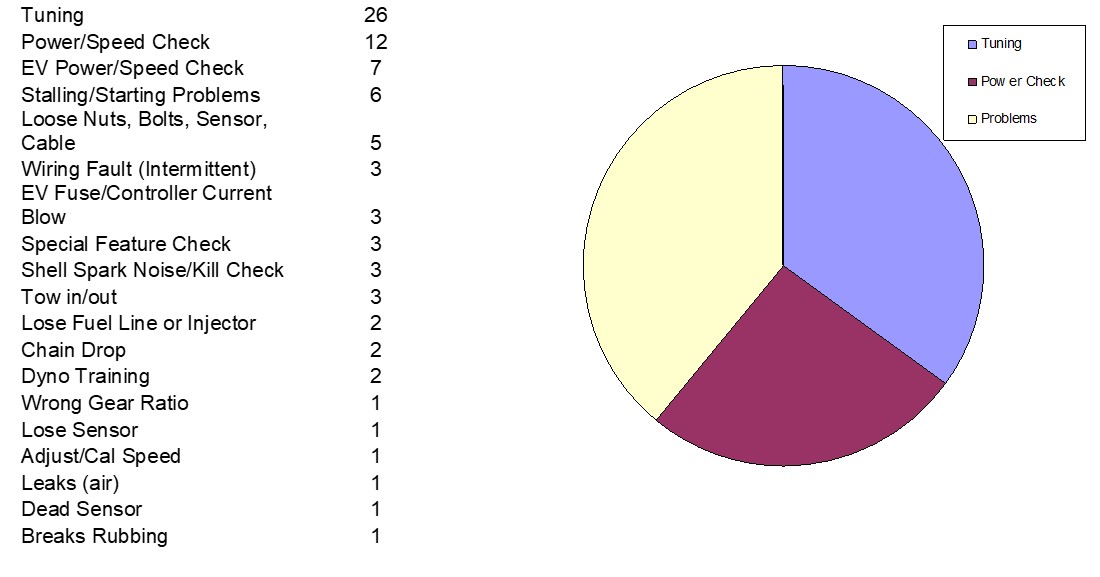
Interestingly one of the teams had a grossly miss-matched transmission with a 6:1 gear ratio. The vehicle actually recorded 130kph on the dyno!
During testing there were 3 instances of pressurized fuel leaks: two caused by the fuel line slipping off the bottle (related with tube warming and loosening: both were properly clamped with a hose clamp) and one when a fatigued exhaust pipe fell onto the fuel line, melting it. These failures would likely have happened on the track, and could have resulted in vehicle fires. Thanks to the safety training none of the cars had any trouble during the dyno test: they were shut down, fuel tap closed, and extinguisher on hand within about two seconds of the occurrences. We are, however, recommending an improvement in the fuel bottle: there should be a larger “head” added to the lower end of the bottle to prevent clamp/hose slippage.
Many of the problems solved on the dyno would have been very difficult to figure out on the track: engine vibrations causing chain drop, loose wiring connections, and above all tuning problems. Having the dyno available for testing allowed teams to fix these problems without clogging up the track queue, blocking traffic, and in a much safer and controlled environment. With this in mind, we believe that dyno testing should take on a larger role in the SEM. One of the major advantages of dyno testing is that it can be done, rain or shine.
Also much of the time was spent with the students reviewing the fundamentals of air/fuel ratio tuning. Being EFI experts is a tremendous help to the student teams.
This shows the exhaust system that failed. It was noted by our engineers prior to failure (thus we have the “before foto on the left). The exhaust system was made from aluminum and cantilevered, resulting in a fatigue failure at the root (right shows failed flange on engine):
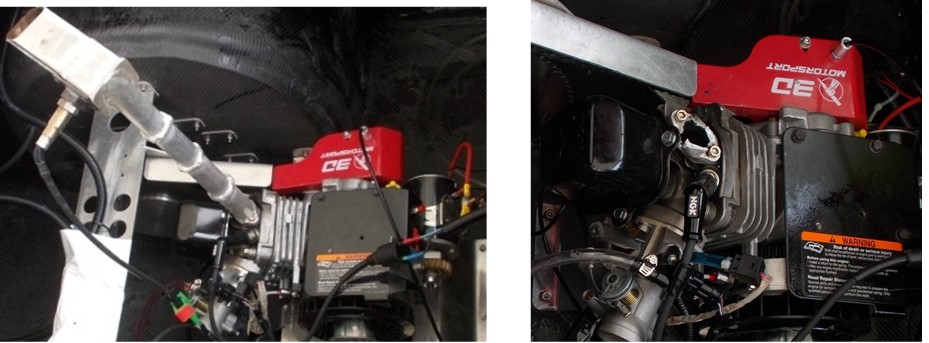
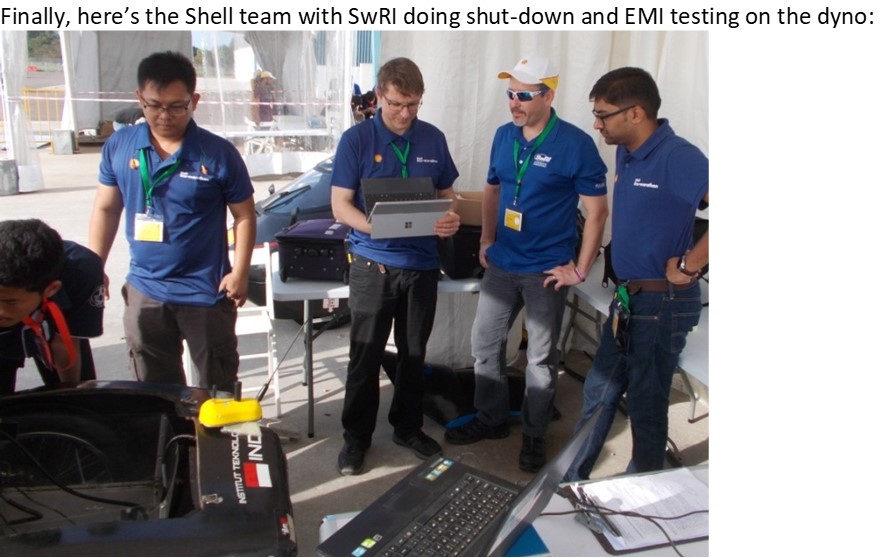